TN 5.10 Integral Bell Transition for HDPE Pipe
Filename:
TN 5.10 Integral Bell Transition for HDPE Pipe.pdf
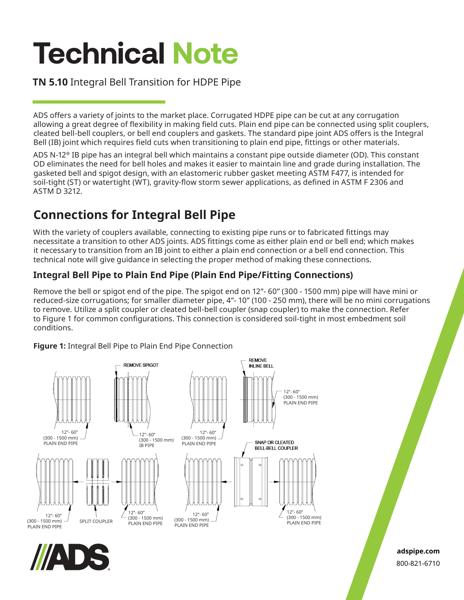
This document is the TN 5.10 Integral Bell Transition for HDPE Pipe. An explanation of connections and vent tube sealing is supported by illustrations.
ADS offers a variety of joints to the market place. Corrugated HDPE pipe can be cut at any corrugation allowing a great degree of flexibility in making field cuts. Plain end pipe can be connected using split couplers, cleated bell-bell couplers, or bell end couplers and gaskets. The standard pipe joint ADS offers is the Integral Bell (IB) joint which requires field cuts when transitioning to plain end pipe, fittings or other materials.
ADS N-12® IB pipe has an integral bell which maintains a constant pipe outside diameter (OD). This constant OD eliminates the need for bell holes and makes it easier to maintain line and grade during installation.
Connections for Integral Bell Pipe occurs with the variety of couplers available, connecting to existing pipe runs or to fabricated fittings may necessitate a transition to other ADS joints. ADS fittings come as either plain end or bell end; which makes it necessary to transition from an IB joint to either a plain end connection or a bell end connection.
Integral Bell Pipe to Plain End Pipe (12” – 60”) (Plain End Pipe/Fitting Connections).
Remove the bell or spigot end of the pipe. The spigot end on 12”-60” pipe will have mini or reduced-size corrugations; for smaller diameter pipe, 4”-10”, there will be no mini corrugations to remove. Utilize a split coupler or cleated bell-bell coupler (snap coupler) to make the connection. This connection is considered soil-tight in most embedment soil conditions.
Integral Bell Pipe to a Welded Bell is explained with supporting welded bell connection photographs.
Integral Bell Pipe to Bell-Bell Coupler Connection is explained and has Bell-Bell Couple Connection figures.
The manufacturing process of corrugated plastic pipe requires the release of hot air from inside the corrugations in order to properly form the corrugations. This hot air is allowed to escape from the corrugations during the extrusion process via vent tubes that run the length of the pipe. Vent tubes become exposed when the pipe is cut in the field to install a fitting, connect to a manhole, or otherwise adjust the length of a pipe run. Exposed vent tubes may result in a leak path, and therefore is recommended that they be sealed.