Thought Leadership
November 1, 2023 / 4 minute read
Reducing Risk in Manufacturing Through Technology and Engineering
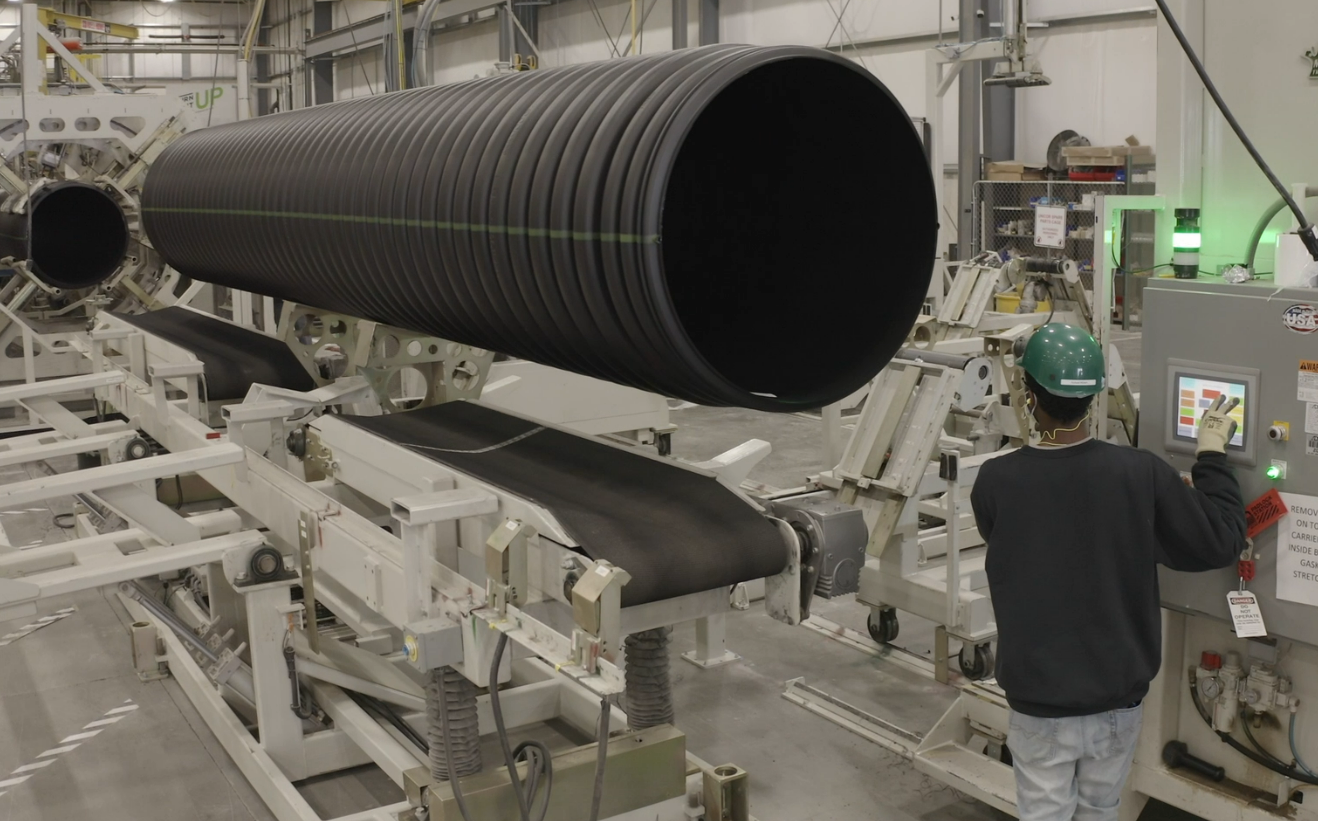
Written by Chakeyla Anderson, VP, Environment, Health and Safety
ADS was founded on the belief that there are more sustainable ways to manage water and protect our environment. But we can’t do that without protecting our people first.
As the vice president of environment, health and safety, I take the responsibility of protecting our team very seriously. That includes mitigating environmental risk from our manufacturing processes, ensuring risk reduction methods are thorough and understood, and having leaders in place who value safety as their number one priority.
Across the country, manufacturers like ADS are conducting or participating in research, identifying new ways of working and developing new technologies and engineering solutions that help to improve operator safety — whether in a manufacturing plant, storage yard, or on the road. In fact, it’s become such an important part of our business, we’re building a new ADS Engineering and Technology Center to continue developing these kinds of safe innovations.
At the operational safety level, that means analyzing and investing in both high- and low-tech engineering solutions, including:
- Visual management systems: A combination of electronic, light, and physical barriers can better identify safe and risky work areas. AI-assisted cameras and software can also monitor for items (or people) that shouldn’t be in a particular area, giving audible warnings or even shutting down lines when needed.
- Integrated automation: ADS has made capital investments in automation systems to help keep our people safe while making, coiling and palletizing pipe, septic and stormwater chambers. These systems allow us to more safely and efficiently run our manufacturing lines 24 hours a day, and by removing the highly manual and physical lifting tasks from our technicians, we’re able to reduce their injury risk.
- Smart personal protective equipment (PPE): This PPE combines traditional gear with electronics and technology and allows for monitoring the location of personnel in the event of an emergency. When connected to forklifts, vehicles, smart cameras and other equipment at the manufacturing site, it can reduce or eliminate collisions and accidents. We’re also piloting smart ergonomics PPE in FY2024 at two plants to help keep our workers injury-free while performing tasks.
For us to be successful in our safety efforts, every ADS employee must be part of our safety team. We recently created a simple assessment checklist that any employee visiting or working in a plant or storage yard can use to look for risks to people and the environment. Rather than a safety team of a dozen or so employees, we now have thousands who know what to look for and how to report issues. Combine that with plantwide software and safety dashboards to better track the organization’s safety performance, we know exactly where to deploy additional safety focus and training.
We’re also implementing advanced technologies and engineering solutions to mitigate the environmental impact of operations. And I believe the biggest and most important environmental protections we’ve made at our plants center on stormwater management to reduce or eliminate the loss of raw material in the form of plastic pellets that end up becoming our plastic pipes. We’ve devised solutions –– concrete berms and stormwater basins –– to capture that plastic and keep it on our property and in the manufacturing process. We added custom pans that catch any spillover from rail cars and utilize ADS’ own highly engineered filters in stormwater drains to be extra sure we keep those pellets out of local water systems.
Employee and environmental safety are key components of ADS’ work, and I’m excited by the progress our industry is making to improve in these areas. If you’ve come across or are implementing other cutting-edge technologies in your business, I’d love to trade ideas and discuss. Reach out to me at chakeyla.anderson@adspipe.com.